Driving Manufacturing Success with Custom KPIs: A Comprehensive Guide
- info856155
- Oct 1, 2024
- 3 min read
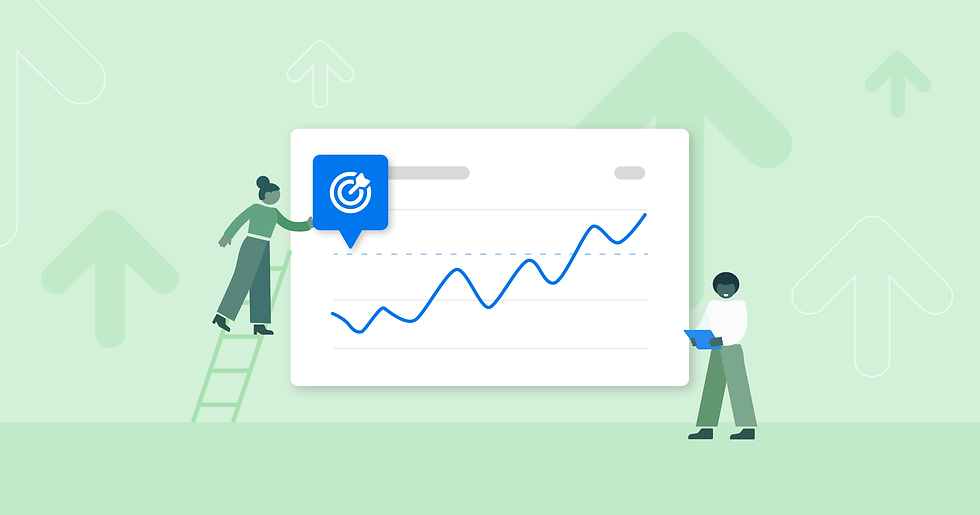
Success in the competitive manufacturing world hinges on more than just productivity; it requires precise, data-driven decision-making. Custom Key Performance Indicators (KPIs) are pivotal in guiding manufacturers toward operational excellence. But how do you design these KPIs to meet the unique needs of your business?
Tailoring KPIs to Your Business Model
Customizing KPIs starts with understanding your specific business model. For example, a manufacturer producing on-demand, precision parts will have different priorities than a company mass-producing consumer goods. Begin by identifying the core areas of your operation that directly impact profitability and efficiency, such as inventory management, production costs, or maintenance schedules.
Inventory Turnover
For a company focused on lean manufacturing, tracking inventory turnover is crucial. A custom KPI here could involve setting a target for how quickly inventory should move through your supply chain. This KPI helps ensure that resources aren't tied up in unsold goods, reducing waste and improving cash flow. To customize this KPI, consider product demand cycles, supplier reliability, and storage costs.
Aligning KPIs with Strategic Goals
Your KPIs should reflect the broader strategic goals of your organization. Whether you aim to reduce production costs, improve product quality, or increase customer satisfaction, each KPI should align with these objectives. For instance, if your goal is to enhance product quality, you might develop a KPI around the rate of defects per production cycle.
Maintenance Cost Management
Maintenance costs can be significant for manufacturers using advanced machinery. A custom KPI could track the frequency and cost of repairs against budgeted amounts. This KPI allows you to predict maintenance needs more accurately, ensuring you're not caught off guard by unexpected expenses. Customization might involve setting different thresholds for various types of machinery based on their age, usage, and maintenance history.
Creating KPIs Based on Data Availability
The effectiveness of a KPI depends on the accuracy and availability of data. Start by assessing what data is readily available within your systems. For example, if you're tracking the actual cost of goods sold, you need access to detailed information about raw material costs, labor, overhead, and waste. Custom KPIs should be built around data that is not only accurate but also regularly updated to provide real-time insights.
True Cost of Goods
Manufacturers often underestimate the actual cost of producing goods. A custom KPI would involve calculating the total production cost, including hidden expenses like utilities, maintenance, and indirect labor. You can identify the most profitable products by tracking this KPI and making informed pricing and production-focused decisions. Customizing this KPI might involve setting up a system to regularly update cost inputs, ensuring the data reflects current market conditions.
Implementing and Reviewing KPIs
Once KPIs are established, it's essential to implement them effectively across your organization. This means communicating their importance to all relevant teams and integrating them into regular reporting and decision-making processes. However, creating a KPI isn't a one-time task; it requires ongoing review and adjustment to remain relevant as your business evolves.
Obsolete Inventory Management
A custom KPI could monitor how extended inventory sits in storage before it becomes obsolete to avoid the costs associated with excess inventory. This KPI might involve setting thresholds for different product categories based on shelf life and demand trends. Regularly reviewing this KPI lets you make proactive decisions about discounting, repurposing, or writing off obsolete stock.
Custom KPIs are powerful tools in the manufacturing industry, enabling businesses to make informed, strategic decisions that drive success. By tailoring KPIs to your specific needs—optimizing inventory levels, controlling maintenance costs, or accurately calculating production expenses—you can enhance efficiency, reduce waste, and improve profitability. Investing in developing and continuously reviewing custom KPIs is not just a best practice; it's a critical step toward achieving operational excellence and long-term growth in the competitive manufacturing landscape.
Visit Esino USA to explore how our innovative products and solutions can help you optimize manufacturing processes and achieve business goals. Don't hesitate to get in touch with our account manager, Zac Marton, at z.marton@esinousa.com for further assistance.
ความคิดเห็น